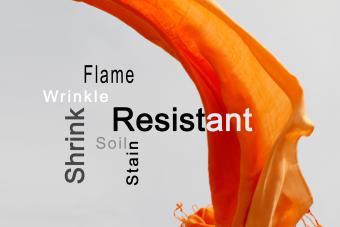
Performance, or functional, finishes are treatments that are applied to woven, knitted, or other textiles to modify their chemical or physical properties. Fabrics can be made to resist shrinking, fading, wrinkling, and soiling. Antimicrobial, antistatic, and water-repellent properties can be added and fabrics can be made more resistant to burning. Most fabrics (or in some cases garments) are treated after dyeing or printing, so that the finish will not interfere with the application of color.
Shrinkage Control
A textile property of significant consumer interest is the ability of fabrics to maintain their dimensions, whether the textile is used in apparel or home furnishings. Shrinkage is a reduction in fabric length or width; growth is a term used for an increase in a fabric dimension. A fabric that neither shrinks nor grows is said to be dimensionally stable. When one considers that a garment with a 25-inch waist will decrease by 1¼ inches if it shrinks only 5 percent, it is understandable that controlling shrinkage has been a goal of textile producers and finishers for many years. Such control has usually involved submitting the fabric to conditions such as moisture or heat that might induce shrinkage, before it is sewn into garments.
Fabrics most susceptible to shrinking during laundering are those that have high moisture absorbance. These include cotton, rayon, linen, and wool. Most synthetics (polyester, nylon, acrylic, and olefin) do not absorb water to a great extent and have higher dimensional stability. Manufacturing of woven or knitted fabrics imposes stresses in the materials as they are stretched and held taut. When the tension is removed and these fabrics are subjected to wetting during laundering, the yarns relax, moving closer together. The amount of relaxation depends on the degree of stretching the fibers underwent during manufacturing and the propensity of the fibers to absorb water and to stretch. Wool and rayon are more extensible than many other fibers and therefore shrink more. Wool has a further problem in that the fibers are covered with scales that can catch and lock together, entangling under conditions of moisture, mechanical action, and heat. This is called felting shrinkage and is the primary reason wool fabrics are not normally washable. These differences in fabrics and fibers point out not only the specification of laundering or dry-cleaning procedures for textiles, but also the need for development of shrinkage-control treatments that are fiber and fabric specific. Compressive shrinkage, the most general control method, is appropriate for 100-percent cotton, linen, or rayon fabrics. In the process, the fabric is dampened and placed on a thick woolen or felt blanket that travels around a small roller. The wet fabric is stretched as it moves around the contour of the roller and then compresses and squeezes as it enters a straight area. Heat is applied to set in the compressed structure. Sanforized and Sanfor-set are trade names for this type of shrinkage-control treatment.
Wool fabrics require special treatments to inhibit both relaxation and felting shrinkage. The former can be controlled by dampening or steaming the fabric and allowing it to dry in a relaxed state. In one variant of this, decating, the fabric is wound on a perforated cylinder and steam is injected. Cold air then sets the relaxed fabric structure. Preventing felting shrinkage allows wools to be laundered. These treatments involve altering the scales on the wool fibers so they do not catch on each other and become highly entangled. One such process degrades the outer scale layer, making the fibers smoother. A preferred method, which runs less risk of degrading the fiber itself, is to mask the scales by applying a thin polymer film.
Synthetic fibers, which are sensitive to heat, can shrink when heat is applied. This phenomenon is apparent when synthetic-fiber fabrics are ironed at too high a temperature. The tendency for heat shrinking can be controlled in finishing by heat setting the fabric at a temperature that allows the molecules in the fibers to relax somewhat. They are therefore less likely to relax further and shrink during the use and care of the textile product.
Wrinkle Resistance
Fabrics made from cotton, rayon, and linen wrinkle easily and will also retain these wrinkles. Cotton and cotton-blend fabrics particularly will often have wrinkle-resistance finishes applied to lessen the need for ironing. These finishes date back to 1929 when cotton fabrics were treated with a chemical compound of urea and formaldehyde to form a polymer resin inside the fiber. The chemical treatment stiffened the fabric, making it "crease resistant."
In the 1950s such treated fabrics, as well as those made from nylon and polyester, which have natural wrinkle resistance, were termed "wash-and-wear." This emphasized that they would not need to be ironed after laundering. Many of these wash-and-wear finishes did, however, require some touch-up ironing.
Further advances in the chemistry of formaldehyde containing finishes produced the permanent-press fabrics of the 1960s and 1970s. Today they are referred to as durable-press finishes in recognition of the fact that the finish is quite durable to laundering but is not permanent. The most frequently used durable-press finish is dimethyloldihydroxyethyleneurea (DMDHEU). The chemical is applied to the fabric and then cured (that is, heated in an oven to react with the cellulose molecules in the cotton or rayon). The reaction bonds the molecules together so that they cannot move around and allow wrinkles to set.
Treated fabrics are cured either before they are fashioned into garments or after. Precured fabrics have their flat shape set in and can be difficult to handle during manufacturing into final textile products. In an alternative postcuring process, the finish is applied to the fabric that is then made into apparel and the curing step occurs subsequently. This allows creases, pleats, hems, and other features to be durably set in the garments.
Soil and Stain Resistance

Soiling can be inhibited by preventing its deposition on the fabric or by facilitating its removal. The range of finishes that includes the patented Scotchgard are examples of the first category. The most effective ones contain fluoropolymers and work similarly to the finish on stick-resistant cookware in repelling stains and soils. The surface energy of the fluoropolymer finish is so much lower than that of liquids that may spill on the fabric that both water-borne and oily soils bead up and do not penetrate into the fibers. These stain- and soil-resistant finishes also provide a degree of water repellency to the treated fabrics. Another general class of stain-resistant finishes is based on silicones. Silicone finishes resist water-borne stains but do not repel oily liquids.
There are also finishes that aid in removing soils and stains that do become attached to fibers. These agents, generally referred to as soil-release finishes, were developed to address the tendency of polyester and durable-press fabrics to absorb and hold oil-borne stains. Water and detergent were not as readily able to penetrate these fabrics and lift out the stains, as had been the case with unfinished-cotton fabrics. The common mechanism of the variety of soil-release finishes is to make them more attractive to water-based detergent solutions. A secondary benefit of soil-release finishes is that, since they attract water, they reduce build-up of static electricity and therefore also serve as antistatic finishes.
Special fluorochemical finishes that confer both soil resistant and soil-release properties are available. These dual-acting finishes are long-chain polymers that have blocks containing fluorine to repel water, oil, and soil, and blocks that attract water. In air, the fluorochemical blocks come to the surface to resist stains. When the fabric is immersed in water, the other, water-loving, blocks are on the surface, enhancing the ability of the fibers to absorb water.
Flame Resistance
Providing some form of resistance to burning has been an objective of fabric finishers for centuries. Early finishes were temporary in that they were removed when the fabrics were laundered. Growing concern for safety in this century brought about federal regulations for required flame resistance for fabrics used in clothing. Local and state laws impose regulations on the flammability of textile materials in public buildings. As a result, durable flame-retardant finishes were developed.
In the literature in this area, a distinction is made between the terms "flame resistant" and "flame retardant." Flame resistant is more general, referring to the resistance of a material to burning. That property can be due to a fiber that is inherently resistant to ignition and/or propagation of flames or can be conferred by application of a finish. In the latter case, the finish is a flame-retardant chemical. Many synthetic fibers shrink from flames and therefore resist ignition. They will burn, however, upon ignition and can be treated to inhibit combustion. Modacrylic is naturally flame-resistant, as are some of the high-performance fibers used today in garments for firefighters and race-car drivers. Cotton and other cellulosic fibers such as rayon and linen will burn readily; they have the same chemical structure as paper. It is these fibers that normally require a retardant finish to make them flame-resistant.
Flame-retardant finishes work either by quenching the flame or by producing char that interferes with the combustion process. Finishes for nylon and polyester contain bromine that reduces the generation of flammable gases. Durable finishes for cotton and cotton-blend fabrics are phosphorus compounds which react chemically with the cellulose fibers and inhibit the production of compounds that fuel the flame.
Other Finishes
Other possible finishes include antimicrobial, light-resistant, mothproof, and temperature-regulating finishes.
Antimicrobial Finishes
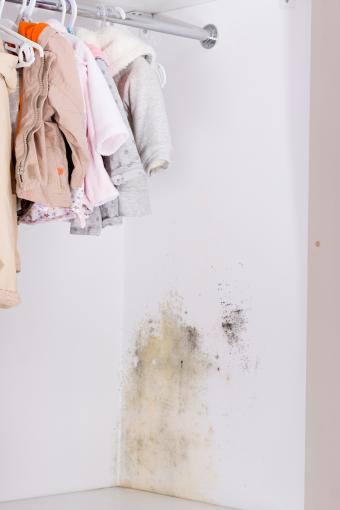
Clothing, particularly soiled clothing, is susceptible to growth of mold, mildew, and bacteria. Not only does the growth of these microbes on fabric present health problems, it also causes odors. Antimicrobial agents to protect against both can also be incorporated into manufactured fibers before they are spun or can be applied as finishes to fabrics. Antimicrobial finishes work either by setting up a barrier against the microbes, preventing them from attaching to the fibers, or alternatively by killing the offending organisms. Agents that kill fungi and bacteria are divided into two general classes; organic materials and compounds containing metals. Copper, zinc, and silver are biocidal metals that have been used on fabrics and clothing items such as socks and underwear. Ammonium salts and phenols are organic compounds that are applied. The active ingredient in Lysol antiseptic spray is a phenolic compound.
Light-Resistant Finishes
The ultraviolet (UV) rays in light can be harmful to clothing fabrics, as well as to the people wearing them. UV light breaks the polymer chains comprising fibers, ultimately weakening fabrics. Some fibers (cotton, rayon, silk, olefin) are more readily damaged than others. The light can also change the structure of dyes, causing fading of fabrics. Light-resistant finishes work either by preferentially absorbing UV radiation that would be harmful to fibers or dyes, or by reflecting such radiation so that the textile does not absorb it. Concerns over the harmful effects of UV light on skin have prompted development of finishes that enhance absorption or reflection. Apparel made from fabrics with these finishes is advertised as having UV or sun-protective qualities.
Mothproofing Finishes
Wool fabrics are damaged by moth larvae, which consume the wool protein, leaving holes in the fabric. Traditionally, wools were stored in bags with mothballs, large pellets containing the ingredient naphthalene that killed the larvae. In the early 2000s, finishes were available for a durable application during fabric manufacturing or a renewable application when wool items are dry-cleaned.
Temperature-Regulating Finishes
Temperature-regulating fabrics are sensitive to the surrounding temperature or to body heat. They are generally referred to as phase changes materials because they change from one phase (solid to liquid or liquid to solid) in reaction to the surrounding temperature. The phase change consumes or releases heat. Polyethylene glycol exhibits this behavior when applied to fabrics. It absorbs and holds heat at high temperatures, cooling the wearer; it then releases this stored heat energy under cooler conditions. The finish has been applied to T-shirts, underwear, socks, and sportswear.
Bibliography
Mark, H., Norman S. Wooding, and Sheldon M. Atlas. Chemical Aftertreatment of Textiles. New York: Wiley-Interscience, 1971.
Slade, Philip E. Handbook of Fiber Finish Technology. New York: Marcel Dekker, 1997.