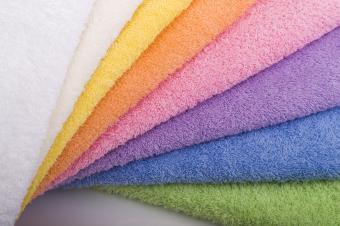
Slack tension weave is part of a family of weaves that rely on a variation in tension between top and bottom sheds to produce design effects on the surface of fabrics. Broadly speaking, terry, plisse, and pile fabrics fall within this definition, but other many other fabrics make use of the principle as well.
Uses
Fabric formation by weaving requires a tension balance between the top and bottom sheds of the warp prior to warp insertion. Common fabrics such as many twills, satins and plain weave variants utilize differences between top and bottom shed tensions to produce more dramatic face or back effects on a fabric surface. These types of shed geometry variations are sometimes colloquially known as "weaving in a sack" because the tension differences are reminiscent of a sack held open at the top while the bottom is allowed to be slack.
Techniques
Slack sheds are produced by a smaller displacement from the horizontal or closed shed position by one shed opening than the other. Usually it is the top shed that is allowed to be slack while the bottom shed is held tight. The limiting factor to the tension in the tighter shed may be determined by one of two rules. In the first rule, the tightest shed may be no more than 10 percent tighter than the base tension of the warp during closed shed. By the second rule, the individual ends of the tighter shed should bear no more than 15 percent of the average single end break load of that warp yarn type.
Within the initial modulus region of the yarn's load-elongation profile, there is direct proportionality of the yarn tension to the shed opening angle. That tension or load may be determined either by dividing the base warp tension at closed shed by the cosine of the appropriate opening angle or it may be found by using the Pythagorean theorem to find the yarn extension during opening. It is important to note that the opening point of the rear shed is determined by the position of the stop motion and not by the whiproll of the weaving machine.
Since warp let-off is governed by reaction of the whiproll or tensioner rolls, the slack shed is advanced by the same length as that demanded by the more heavily loaded shed. As a result, longer floats are generated in the fabric than would be present in symmetrical shed weaves. These long floats create structural variations on a fabric surface that are utilized by designers to produce billows, waves, rows and similar textures.
Variations
Other variants of slack shed weave designs require the use of multiple warps advancing at different rates from different warp beam let-off systems on the same machine to produce pile and loop effects on the surface of a fabric. Such systems require exact feed measuring for the warps and often require variable beat-up systems to compact the picks into a warp of deliberately varying lengths.
See also Loom; Double Weave; Pile Weave; Plain Weave; Satin Weave; Twill Weave; Weaving; Weave Types; Weaving Machinery.
Bibliography
Emery, I. The Primary Structures of Fabrics. Washington, D.C.: The Textile Museum, 1980.
Gioello, D. A. Profiling Fabrics: Properties, Performance, and Construction Techniques. New York: Fairchild Publications, 1981.