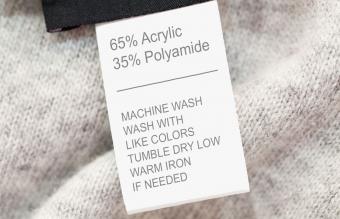
Acrylic and modacrylic fibers are produced from acrylonitrile, a petrochemical. The U.S. Federal Trade Commission defines fibers of 85 percent or more acrylonitrile units as acrylic fibers: for modacrylics the figure is 35-85 percent. Early fibers were based on 100 percent acrylonitrile, but more successful versions were produced by the inclusion of up to 15 percent of other chemical units that improved the ability of the resulting fiber to absorb dyes. In the 1950s, a golden age of new synthetic fibers, acrylic fibers became well known under trade names such as Orlon, Acrilan, Zefran, Creslan, and Courtelle: modacrylics included Dynel, Teklan, and Verel.
Acrylics Vs. Synthetics
The variability of chemical composition, together with differences in fiber production methods, mean individual versions of acrylic fibers differ from each other more than other synthetic fibers. Likewise, many different modacrylic fibers have been produced, although they tend to contain considerable amounts of chlorine-based units. This chlorine component provides the flame-resistant properties of modacrylics. The market share of both acrylic and modacrylic fibers has declined somewhat since the 1980s, and although generically separate, it is appropriate to discuss them together.
Acrylic fibers have round or moderately irregular cross sections typically characterized as bean, dog-bone, or peanut shaped. A given volume of fiber is comparatively lightweight (fiber density is 1.17). Acrylic fibers are approximately half as strong as nylon or polyester (tenacity is 2-3.5 g/d), and they have limited use where strength is a major requirement. Like most synthetics, they absorb little water (moisture regain is 1-2 percent), and acrylic fiber materials are quick drying. Fibers recover well from small amounts of stretching. They have excellent resistance to sunlight and weathering and to a wide range of chemicals, particularly inorganic acids. They are thermoplastic, softening at 450-500°F (230-260°C), and can be heat set and texturized, although excessive heat will cause yellowing. Modacrylics have similar properties except a higher density (~1.35), softening temperatures that are 50-100°F lower, and the "self-extinguishing" flame response that comes from the chlorine content.
Dyeing Acrylic Fibers
The variable chemical units in the fiber allowed for fibers of differing dyeing behavior, and some were produced to be dyeable with acid dyes, as wool is. In the early 2000s, most acrylic fiber variants are dyed with basic (cationic) dyes. Many early synthetic dyes (including Perkin's Mauve were basic dyes, and these were adopted for acrylics, but dyemakers later developed "modified" basic dyes specifically for use with these fibers. Disperse dyes may also be useful for pale shades. A considerable amount of acrylic and modacrylic fiber is colored during manufacture, either as "solution dyed" fiber or by applying dye to the fiber immediately after spinning in "gel-dyeing."
Most acrylic is produced as staple fiber, and bulky yarns are generated from blending fibers of different shrinkage properties. Fibers made from two different acrylic materials ("bicomponent fibers") produce especially bulky fibers and yarns. As the ease of creating bulky yarns suggests, and the suffix "-lan" or "-lon" implies, the fibers find favor in wool-like end uses: sweaters, blankets, socks, knitting yarn. In microfiber versions, acrylics make very soft scarves. Flammability issues and a lack of resilience has limited application of acrylic fibers in carpets. For many years, sweatshirts and pants were based on blends of cotton and acrylic fibers: polyester has now taken over the synthetic role in that end use. Modacrylic and acrylic fibers make the most successful fake furs and are widely used in hairpieces and doll hair. The superior sunlight resistance of both fibers makes them useful for outdoor applications such as awnings, with modacrylics providing additional flame resistance. The low flammability of modacrylics provides a measure of safety despite the low softening temperature: end uses based on this property have included airline blankets and military sweaters. Acrylic fibers are used as starting materials in the production of carbon (graphite) fibers.
Acrylic Fabric Care
Articles made of acrylic fibers are easy to care for: they dry easily and, if properly set during manufacture, maintain their dimensions. Excessive conditions may cause loss of bulk or shrinkage. Acrylic and modacrylic fibers are now mature: cheaper polyester has taken over several of their end uses.
Bibliography
Adnaur, Sabit. Wellington Sears Handbook of Industrial Textiles. Lancaster, Pa.: Technomic, 1995.
Burkinshaw, S. M. Chemical Principles of Synthetic Fibre Dyeing. Glasgow, New York: Blackie Academic and Professional, 1995.
Cook, Gordon J. Handbook of Textile Fibres, Part 2: Man-Made Fibers. 5th ed. Durham, U.K.: Merrow, 1984.
Moncrieff, R. W. Man-Made Fibres. 6th ed. London: Newnes-Butterworth, 1975.